Hypervelocity, as defined by the U.S. Army, refers to a projectile leaving the muzzle of an artillery weapon at over 3,500 ft/s (1,067 m/s) or a tank cannon at more than 3,350 ft/s (1,021 m/s). It’s important to note this isn’t the same as hypersonic speeds, which exceed Mach 5 (1,715 m/s). Tank gun kinetic energy projectiles fall under the hypervelocity category, and now there are specialized hypervelocity projectiles in development for artillery weapons.
Hypervelocity projectiles are designed for speed, typically lightweight and highly aerodynamic. These projectiles include subcalibre kinetic energy penetrators fired from tank main guns, although the term “hypervelocity” is not commonly used today. It was more prevalent during and shortly after World War II.
The technical term for tank-fired subcalibre kinetic energy projectiles is APFSDS (Armor Piercing Fin Stabilized Discarding Sabot). In the US Army, tank crews refer to these rounds as “Sabot,” while British tankers call them “Fin” rounds. German tank crews use the terms “Treibspiegel” or “Treibkäfig,” and in Finland, they are simply known as “Alikali,” meaning subcalibre (“Alikaliiperinen”).
BAE Systems is currently developing long-range Hypervelocity Projectiles (HVP) that can be deployed by both land and naval artillery. These projectiles are maneuverable and guided to their targets. They can also be used to intercept incoming anti-ship missiles, offering a cheaper alternative to conventional missiles, with the added advantage of being fired at a rapid rate.

Large Calibre Kinetic Projectiles
German company Rheinmetall manufactures some of the most advanced large-calibre kinetic energy projectiles, which are the primary ammunition used against enemy main battle tanks (MBTs).
Modern kinetic energy ammunition is known as APFSDS, short for Armor Piercing Fin Stabilized Discarding Sabot. These subcalibre projectiles have a full-calibre sabot around them to centre the penetrator in the barrel during the firing process. Since they are fired from smoothbore guns, APFSDS rounds are stabilised by fins rather than by spinning around their longitudinal axis.
Kinetic energy penetrators are made from heavy metals such as depleted uranium (DU) and tungsten heavy alloys (WHA). Depleted uranium undergoes natural adiabatic shear failure at the tip, creating a smaller cross-sectional penetration cavity compared to tungsten, which aids in achieving greater penetration depth.
Advances in metallurgy and manufacturing of WHA alloys are ongoing. By doping WHA alloys with rare earth metals, they can be made to fail via adiabatic shear, though whether this has been implemented in current designs remains unknown.
Rheinmetall is currently developing a new penetrator for their higher-pressure Rh-120 L55A1 tank gun, called the KE2020Neo. This new projectile is expected to improve performance by around 20% compared to the current generation, likely referring to increased penetration into Rolled Homogeneous Armour Steel (RHA).
This improvement comes from a lighter sabot and more energetic propellant, made possible by the higher chamber pressure of the L55A1 gun. The KE2020Neo penetrator, made from tungsten alloy, is expected to be ready by 2026. It is thought that the KE2020Neo could max out the penetration potential of the Rh-120 L55A1 gun, with the next logical step being a shift to the larger 130mm calibre tank gun being developed by Rheinmetall.
In designing subcalibre kinetic projectiles, they cannot be made too slender (in terms of the length-to-diameter ratio), as this would reduce their effectiveness against heavy reactive armour. This type of armour uses thick, explosive-propelled metal plates that disrupt the penetrator’s structural integrity and flight path by transferring momentum to it.
Kinetic energy penetrators are always optimized to defeat specific enemy tank armour configurations. Some may include functional segments designed to counter specific layers within the enemy’s armour.
Supersonic Design

The nose shape of a projectile plays a significant role in reducing the drag coefficient, thereby minimizing velocity loss over distance traveled. Slender ogive shapes provide the lowest possible drag coefficients at high velocities, and the velocity regime in which the projectile operates determines the exact optimum nose geometry.
The projectile’s fineness ratio also plays a critical role in reducing drag at supersonic velocities. Increasing the fineness ratio significantly reduces drag by lowering the wave drag coefficient, with only a marginal increase in skin friction.
Improved performance can also be achieved with a sharper nose shape. However, for thermal management, practical solutions often feature a small-radius blunt section at the tip, which creates a detached shock wave or bow shock. This reduces the heat flux to the projectile body, addressing the issue of aerodynamic heating, particularly with high-supersonic and hypersonic projectiles.
The fineness ratio is calculated by dividing the projectile’s nose length (L) by its caliber (D), resulting in the L/D ratio. Typically, there is no significant reduction in drag coefficient when increasing the fineness ratio beyond 5:1 or 6:1 at high supersonic speeds.
A third important design aspect is boat-tailing the aft (base) section of the projectile. This helps reduce base drag, which results from the low-pressure region forming at the projectile’s rear. At supersonic speeds, the optimal boat-tail angle is smaller than at subsonic speeds, though the effectiveness of boat-tailing decreases as the Mach number increases.
Theodore von Kármán: Minimum drag
Theodore von Kármán (1881-1963) was a Hungarian-American scientist who specialized in aerodynamics and flight technology. He made one of the earliest theoretical attempts to determine the minimum drag nose shape, deriving an integral equation for the wave drag of slender bodies of revolution at moderate supersonic speeds.
Von Kármán's work was later extended by researchers like Sears and Haack, leading to the development of what is now known as the Sears-Haack shape, the theoretical optimum nose shape for slender ogives at moderate supersonic speeds.
BAE Systems HVP Analysis
The BAE Systems Hypervelocity Projectile (HVP) is an ultra-long-range guided artillery shell designed to hit moving targets. It can be fired from various platforms, including land artillery, naval guns, and electromagnetic (EM) railguns.
From the shape of the HVP, it’s clear that it has been optimized for high supersonic and hypersonic speeds. The nose of the projectile appears to follow a von Kármán or Sears-Haack profile, or something similar, with a small-radius blunt tip for thermal management.
The HVP boasts a high fineness ratio (the ratio of nose length to projectile calibre), making the entire projectile appear as one extended nose shape, with seemingly no cylindrical body section at all. Based on available photos and schematics, the fineness ratio of the HVP is approximately 7:1.
According to certain scientific sources, the nose of the HVP is made from tungsten, which makes sense given the need to withstand the aerodynamic heating that occurs at high supersonic and hypersonic speeds. Tungsten’s high melting point allows it to absorb significant amounts of heat. There may also be a short boat-tailed section at the rear of the projectile to reduce base drag, as seen in images from BAE Systems’ website, though this feature doesn’t appear in the models displayed at military exhibitions.
BAE Systems has released technical specifications for the HVP. The total length of the integrated launch package is 26 inches (660.4 mm), with the flight body itself measuring 24 inches (600.0 mm). The weights are 40 pounds (18.2 kg) for the full package and 28 pounds (12.7 kg) for the flight body. The HVP carries a 15-pound (6.8 kg) payload, which constitutes 54% of the total projectile mass. The table 1 (see below) provides range data for different weapons platforms.
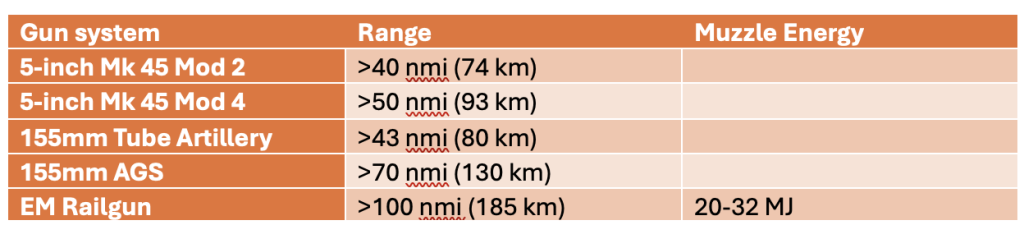
Railgun Development During World War II
In 1944, Germany proposed the first electromagnetic railgun during World War II. It was intended to be an electric anti-aircraft gun with a longer range than conventional propellant-based weapons. The power required for its operation was estimated to be half of what was needed to power the entire city of Chicago at the time.
Germany initiated two railgun projects during the war. The first was designed to bombard London, and the second was an anti-aircraft gun. The so-called "London Gun Railgun" was expected to have a range of 248 kilometres, capable of firing a 204.5-kilogram projectile. However, this project was abandoned after being deemed impractical.
The second project, the electric anti-aircraft gun, advanced to the testing phase but was incomplete by the time the war ended. This railgun was intended to fire a projectile carrying 500 grams of explosives at a muzzle velocity of 1,829 m/s. Initial tests were conducted in Berlin and later in the Alps.
After the war, the prototype anti-aircraft railgun was seized by the Americans.
Outperforming Ramjet Artillery
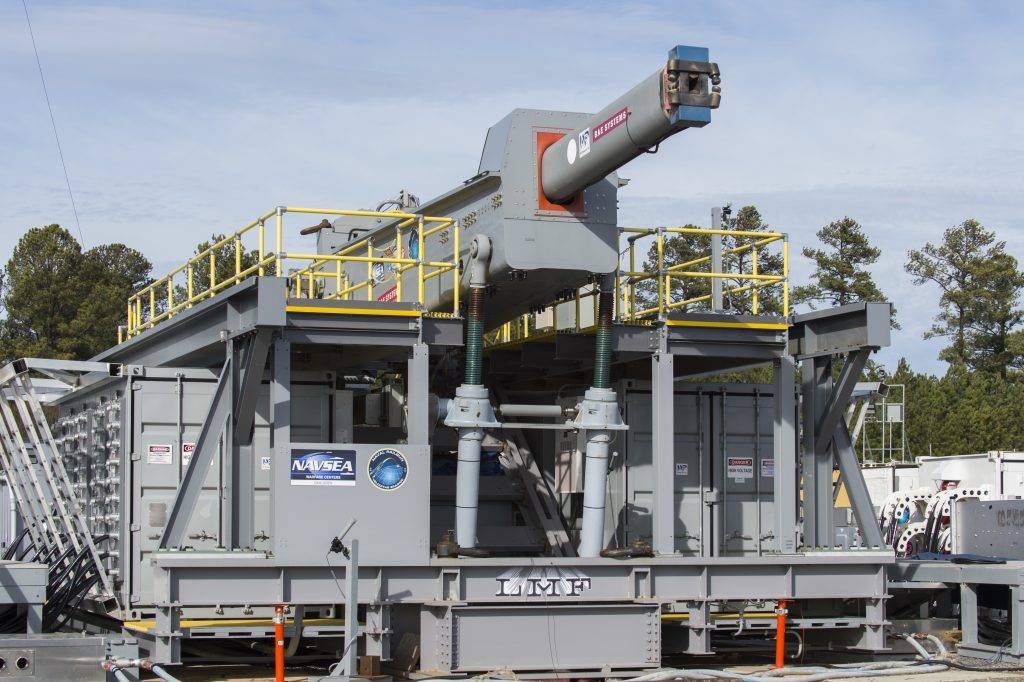
The BAE Systems Hypervelocity Projectile (HVP) has significant potential to become the ultimate long-range artillery projectile, as its range is limited only by the energy the weapon system can provide, and the challenges posed by aerodynamic heating.
The HVP outperforms ramjet-propelled artillery shells in range, though this does not render ramjet projectiles obsolete. Ramjet propulsion offers a different approach to achieving range superiority in combat. However, it’s important to note that ramjet artillery shells cannot be fired from electromagnetic (EM) railguns, as the muzzle velocities are too high for the ramjet to function properly.
In the future, NDR plans to calculate the ranges of the Hypervelocity Projectile with different levels of muzzle energy. One intriguing question is: how far could the HVP fly if its integrated launch package were supplied with 120 megajoules of muzzle energy?
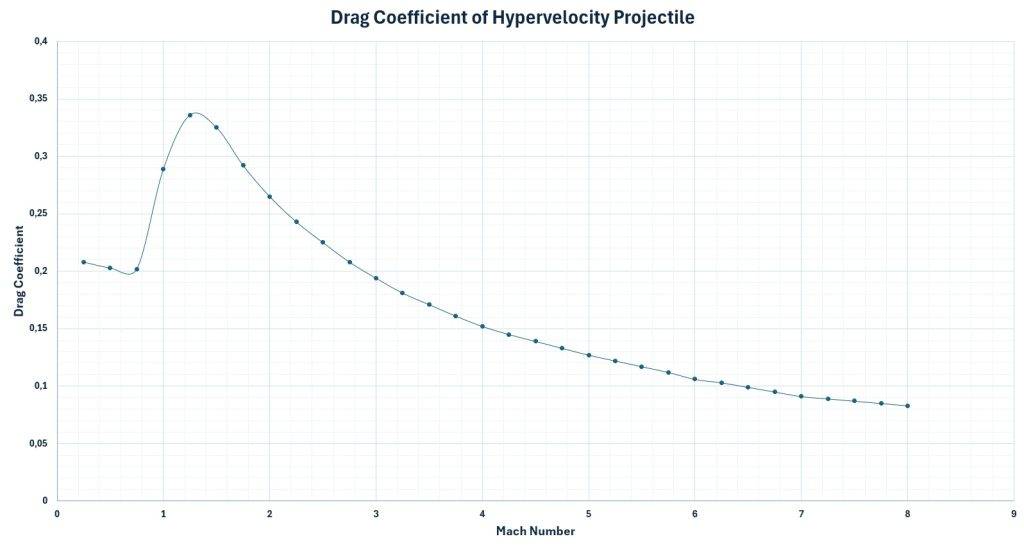
Read More:
- Rheinmetall Waffe Munition GmbH: Large Calibre Weapons and Ammunition
- BAE Systems: Hypervelocity Projectile
- Nammo: The Range Revolution